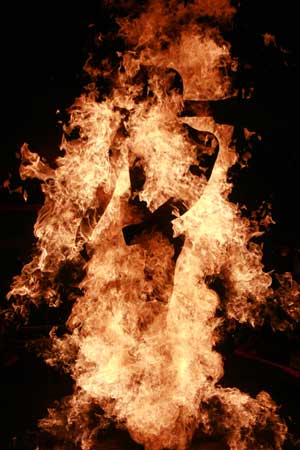
Brian Shiels Textile protection and Comfort Center
PyroMan and Coppelius spend their days at the Textile Protection and Comfort Center on fire. They work in flames alongside students and faculty to test technology that provides fire-fighting gear and materials.
“PyroMan is a thermal mannequin equipped with 122 Pyrocal sensors, which were developed at T-PACC a few years ago,” Kevin Ross, a research assistant at T-PACC, said. “The mannequin is dressed with whatever gear is to be evaluated and then eight industrial burners are ignited to engulf it in flames for up to 12 seconds.”
According to Ross, these results are used to determine if a person wearing these garments would have no burn damage.
The National Fire Protection Association and other organizations have minimum requirements for personal protective equipment. One of these is that a garment not be allowed more than a certain percentage of total body burn after being exposed to a thermal mannequin.
Coppelius is a different kind of mannequin; he is a sweating thermal mannequin — one of only two in the world.
“He is heated, but not set on fire. Coppelius is used to evaluate various ensembles for measurements of comfort and risk of heat stress,” Ross said.
The main role of a flame-retardant textile is to break the chain reactions in fire extinguishing the flame or reducing the burning rate, according to Pratik Ichhaporia, a doctorate student in fiber and polymer science.
“In plastics and textiles industries the major interest is not in the fact that a product burns, but how to render them less likely to burn,” Ichhaporia said. “And if they are ignited, to burn less efficiently.”
Most fire-proof materials can be classified as either being flame-retardant or flame-resistant.
“The term fire-retardant is usually used for chemicals that make materials fire-proof. Fire-retardant materials will burn, albeit very slowly, fire-resistant will not,” Peter Hauser, director of graduate programs and associate head of the textile engineering chemistry and science department, said.
Fire-resistant materials, or permanently fire-retardant materials, are constructed from fibers that are non-combustible for the material’s entire lifetime, according to Ross.
Examples of fire-resistant materials are Nomex or Kevlar, where the material doesn’t burn. Fire-retardant materials generally burn but are treated with a chemical finish.
“Firefighter gear is going to be constructed of something that is inherently fire-resistant,” Ross said. “Both the outer shell and the thermal, insulation layer will be constructed of some type of non-combustible material.”
Hauser said that certain bromine or phosphorous-based chemicals are used to make materials fire-retardant. Similar materials are also used in firefighting gels and sprays, and some of these gels are polymers that hold water.
But chemicals containing bromine are now suspect, according to Hauser.
“The most important issue in fire-retardant or fire-resistant research right now is the environmental issue with the use of bromine-containing chemicals,” he said.
“The European Union is banning certain bromine chemicals now because they persist in the environment and have been found in animal tissues. I suspect that all bromine chemicals will be eventually forbidden.”
The latest ideas for textile flame retardants are intumescent materials, which are materials that foam when heated.
“Intumescence can be described as fire-retardant technology, which causes an otherwise flammable material to foam, forming an invisible barrier when exposed to heat,” Ichhaporia said. “During intumescence, the amount of fuel is also greatly reduced and char, rather than gases, is produced.”
The char produced has a special, active role in fire-protection. It forms a two-way barrier — hindering the passage of combustible gases and molten polymer to the flame, and the insulation and shielding of the polymer from the heat of the flame, according to Ichhaporia.
As far as N.C. State’s contributions are concerned, Ross believes that T-PACC is at the forefront of research in related areas.
“Here at T-PACC, we do a lot of work with fire-retardant/resistant materials and testing them,” he said. “We have received a lot of attention for our efforts in developing a new firefighter turnout system that incorporates chemical and biological protection into the gear.”
Hauser also said that T-PACC is working with the Department of Homeland Security to develop fire-retardant materials and chemical and biological suits for first responders.